- Solar advice hub
- Solar-energy
- What are solar panels made of?
What are solar panels made of?
Discover the key materials that make up modern monocrystalline solar panels, what role each material plays, and where these materials usually come from.
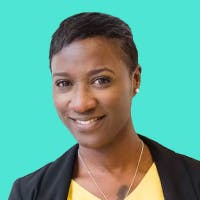
Why you can trust our content
We know that the solar industry is full of misinformation, but we only use reliable sources, including:
- Our experienced solar experts, installers and system designers
- Our own database of solar & battery system designs
- Authoritative bodies like MCS and the UK government

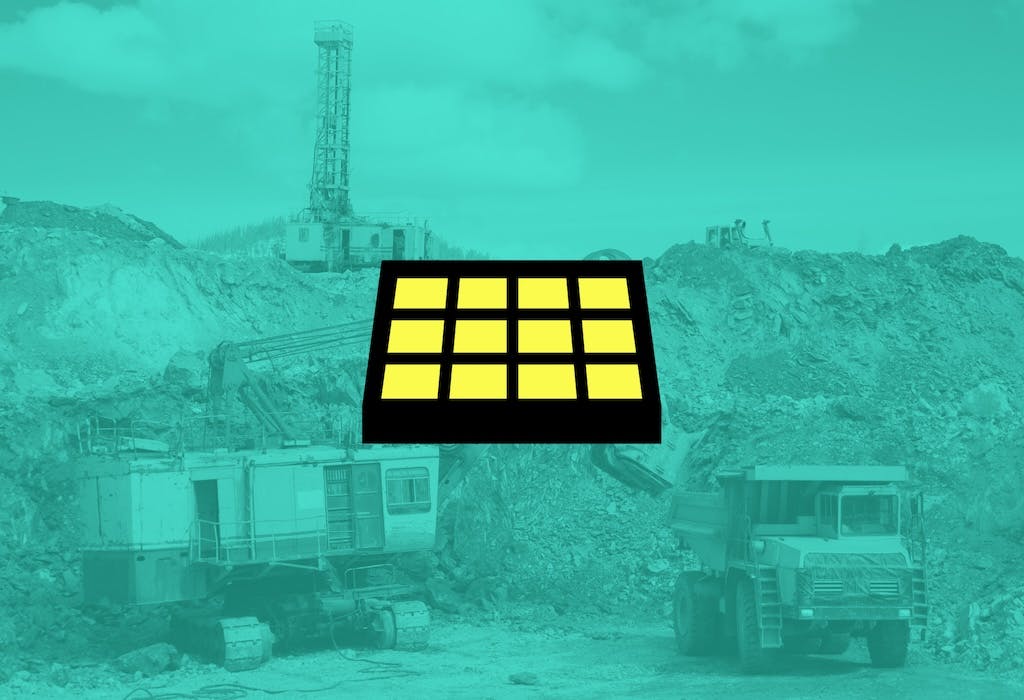
Calculate savings
What kind of home do you live in?
Calculate savings
What kind of home do you live in?
At a glance
Solar panels are an impressive feat of modern engineering, using a varied mixture of materials to convert daylight into electricity. And every piece plays a crucial role - from the polysilicon and metals to the glass and plastics.
This guide will break down the key materials that make up a standard monocrystalline solar panel, along with their respective functions and significance.
If you’re wondering how much a solar & battery system could save you, answer a few quick questions below and we’ll provide you with an estimate.
What materials are solar panels made of?
This guide focuses on single crystal (c-Si) solar photovoltaic (PV) technology, also known as monocrystalline solar panels, which dominate the global solar market. In 2023, 98% of global PV shipments were mono c-Si, a significant leap from just 35% in 2015.
While other technologies like thin-film and perovskite solar panels exist, they remain a sliver of the market, with perovskite still in its experimental phase and not yet widely produced.
Monocrystalline solar panels: materials breakdown
This table details what's inside a monocrystalline solar panel, using research from a 2020 study by the International Energy Agency's Photovoltaic Power Systems Programme (IEA PVPS).
Material | Percentage of monocrystalline solar panel |
---|---|
Polysilicon | |
Aluminium | |
Copper | |
Lead | |
Tin | |
Silver | |
Ethylene vinyl acetate | |
Polyvinyl fluoride | |
Polyethylene terephthalate | |
High-density polyethylene | |
Silicone | |
Solar glass | |
Total |
Silicon metal
Silicon metal, also known as metallurgical grade silicon, is a crucial raw material in solar panel production. Its purified form is the foundation for polysilicon (see below), which eventually gets processed into ingots, wafers and - ultimately - solar cells.
Silicon is derived from silica, which is essentially quartz (or sand), i.e. the most abundant mineral in the Earth’s crust. It's extracted through a high-temperature reduction process in electric arc furnaces.
Global silicon metal manufacturing capacity reached 9.7 million metric tons per year in 2024, with China cornering 76% of the market at 7.4 million tons annually. Major Chinese companies, such as Tongwei Group, are expanding production, with plans to build two plants in Inner Mongolia.
Polysilicon
Percentage of a monocrystalline solar panel: 5.2%
Polysilicon, made from silicon metal, is the key material used to make solar cells. This is because its semiconducting properties allow it to convert sunlight into electricity (i.e. the photovoltaic effect).
While the name might suggest polysilicon is only for polycrystalline solar panels, it's essential for all crystalline silicon solar cells - including highly efficient monocrystalline ones.
Notably, the solar panel industry was responsible for over 98% of polysilicon production in 2023. Like silicon metal, most polysilicon is produced in China. The country upped its global production share to 92% in 2023, up from 86% in 2020.
Improvements in solar cell technology have reduced the quantity of polysilicon needed per watt (W), falling from 2.7g/W in 2021 to 2.2g/W in 2023, which is reflected in lower solar panel prices.
Other metals
Solar panels contain trace amounts of various metals that are crucial for electrical conductivity and structural support. However, accessing these metals means mining, which pollutes habitats and has a significant environmental impact.
To tackle these challenges, researchers are developing solar panels that use less metal but still maintain their high efficiency. Environmental benefits aside, this approach will also make solar power more affordable and sustainable over time.
Let’s explore the key metals found in solar panels and the various roles they play.
Aluminium
Percentage of a monocrystalline solar panel: 0.38%
Aluminium is lightweight, durable, and resistant to corrosion - all of which make it ideal for withstanding harsh outdoor environments. During solar panel manufacturing, it gets added to the backsheet for strength, conductivity, and heat dissipation. It's also used for the solar panel frame, but more on that later.
As of 2023, major aluminium producers include China (41.5 million tons), India (4.1 million tonnes), Russia (3.8 million tonnes), and Canada (3 million tonnes).
Additionally, aluminium’s recyclability supports the industry’s sustainability goals, with recycled aluminium potentially meeting 21% of solar PV demand by 2040. This makes it a critical material in the global transition to renewable energy.
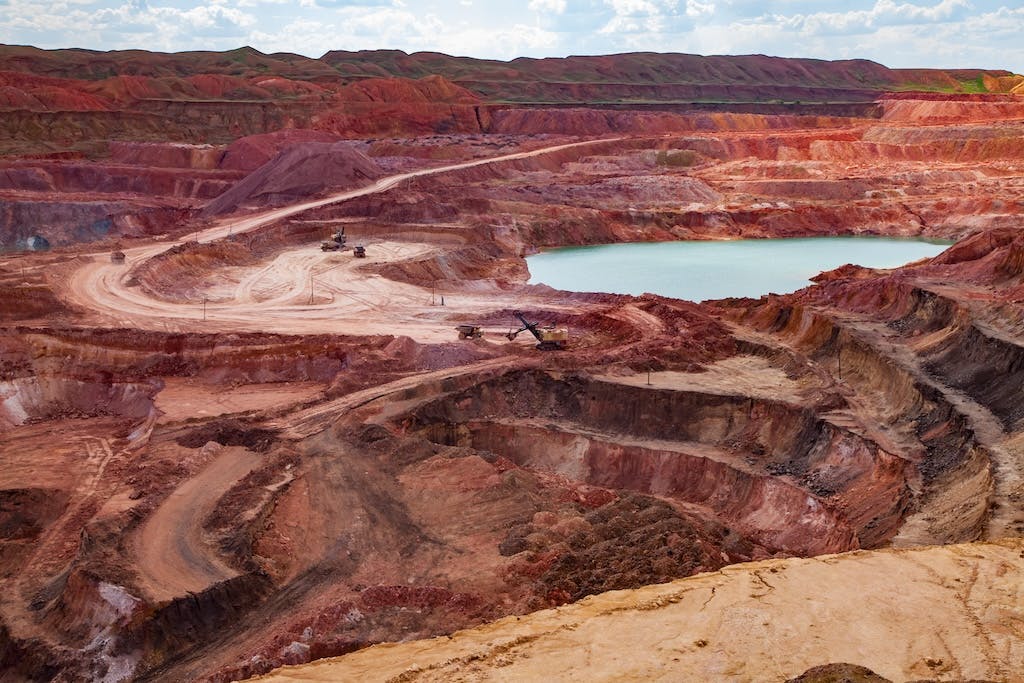
Copper
Percentage of a monocrystalline solar panel: 0.93%
Copper is a key component of the wiring between the solar cells within a solar panel, as it enables optimum electricity flow. Its excellent conductivity properties ensure efficient electricity transfer and effective heat dissipation in solar cells.
Solar power systems can contain approximately 2.3 tonnes of copper per megawatt (MW) of power generation. And according to S&P Global, the demand for copper in solar applications is projected to rise by 11.9% each year between 2021 and 2035.
The main copper-producing countries are Chile (5 million tonnes), Peru (2.6 million tonnes), and the Democratic Republic of Congo (2.5 million tonnes).
Lead
Percentage of a monocrystalline solar panel: 0.01%
In solar panel manufacturing, lead is typically combined with tin to form an alloy used in soldering to connect various components. The metal is flexible with a low melting point, making it ideal for creating electrical connections within the panels.
Lead use in solar panels is decreasing because of established environmental and health concerns, and the industry is shifting towards lead-free alternatives, with some manufacturers already offering lead-free solar panels.
Researchers are also working on lead-free perovskite solar cells, as lead is currently a key component that contributes to their high efficiency and stability. To learn more about this new technology, check out our full guide to perovskite solar panels.
Tin
Percentage of a monocrystalline solar panel: 0.12%
Manufacturers use tin, along with lead, in the soldering process to connect solar cells via solar ribbons (copper wires coated with tin solder). Tin oxide also gets used as a transparent conductive layer to increase the solar panel's efficiency.
In 2023, the main tin-producing countries were China (68,000 tonnes), Myanmar (54,000 tonnes), Indonesia (52,000 tonnes), Peru (23,000 tonnes), and the Democratic Republic of Congo (19,000 tonnes).
The International Tin Association (ITA) estimates that the solar industry used over 22,000 tonnes of tin in 2022, which is a whopping two and a half times what was used in 2019. The rapid deployment of solar installations worldwide and the push for more sustainable and efficient solar solutions are fuelling this growth.
Tin is also gaining importance in next-generation solar technologies, especially in tin-based perovskite solar cells, which offer a promising lead-free alternative.
Silver
Percentage of a monocrystalline solar panel: 0.03%
Manufacturers use silver as a conductive paste to create electrodes on both sides of silicon wafers, which are then dried and fired to form the essential conductive pathways for collecting and transporting electrical currents.
Silver's low electrical resistance means less energy gets wasted, making solar cells more efficient overall.
In 2023, the top silver-producing countries were Mexico (202.2 million ounces, or about 24% of global production), followed by China and Peru (each accounting for about 13% of total production). Other significant producers include Chile, Australia, Poland, Bolivia, Russia, the United States, and Argentina.
Silver usage in solar panels is increasing, driven by advancements in solar technology. By 2030, solar panels could consume about 20% of the total silver supply, up from 13.8% in 2023.
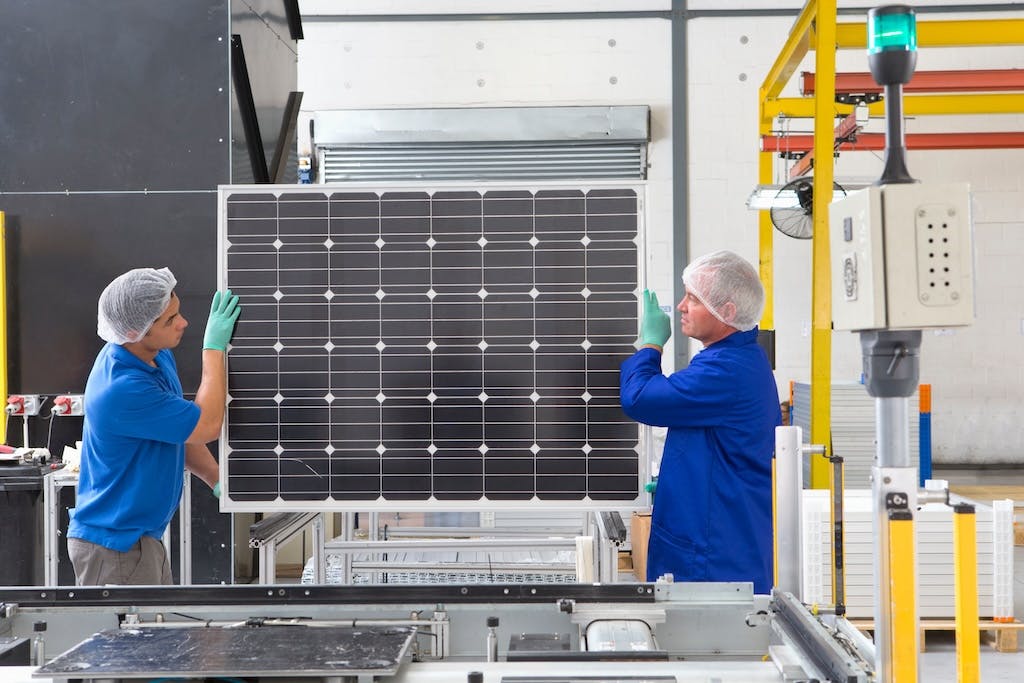
Plastics
Metals get most of the attention in conversations about solar panel production, but plastics are just as essential. They protect delicate solar cells from environmental factors like moisture, UV radiation, and mechanical stress.
Let's dive into the key types of plastics found in solar panels and their specific uses.
Ethylene vinyl acetate
Percentage of a monocrystalline solar panel: 7.94%
Ethylene vinyl acetate (EVA) is a flexible, transparent plastic material used as an encapsulant in solar panels. An encapsulant is a special coating that protects and secures the solar cells, acting as a cushioning layer between the front glass, solar cells, and the backsheet.
EVA gets added during the solar panel manufacturing process by layering sheets of the material above and below the solar cells. These layers are then heated and laminated, causing the EVA to soften and bond tightly to the cells and the other panel components. This process creates a durable and weather-resistant seal.
Solar panels need EVA for resilience against external stresses. However, the coating can degrade over time when exposed to high temperatures and UV radiation - and that can affect the solar cells' performance.
To learn more about solar panel degradation, check out our guide to how long solar panels last.
Polyvinyl fluoride
Percentage of a monocrystalline solar panel: 1.01%
Polyvinyl fluoride (PVF) is a durable thermoplastic polymer commonly used in the solar panel's backsheet. During the manufacturing process, PVF bonds to other layers, like polyethylene terephthalate (PET), to create a robust protective layer on the back of the solar panel.
PVF is great at preventing contaminants (such as moisture and dirt) from entering the panels, keeping its internal components from external damage. It also has good electrical insulation, which reduces the risk of short circuits.
This material is key to a longer-lasting panel. It keeps it strong and safe, even under harsh conditions.
Polyethylene terephthalate
Percentage of a monocrystalline solar panel: 3.13%
Polyethylene terephthalate (PET) is another core material in a solar panel's backsheet. It strengthens and insulates the cells, as well as providing thermal stability, which protects the internal components from environmental stress.
During the manufacturing process, PET typically forms the central layer in a multi-layered backsheet. It gets sandwiched between outer layers of protective materials, such as PVF (see above) or other durable plastics, using lamination techniques. This process creates a composite backsheet that offers robust protection, insulation, and flexibility.
High-density polyethylene
Percentage of a monocrystalline solar panel: 0.22%
High-density polyethylene (HDPE) is a strong, lightweight, and easily recyclable plastic used for mounting structures and protective components, rather than directly within PV cells.
Manufacturers use injection moulding or extrusion to shape HDPE into protective casings, cable management systems, or structural components for solar panels.
Although it isn't a primary material in the PV process, HDPE is critical for protecting and stabilising solar panels in outdoor environments, as it's highly resistant to moisture, chemicals and extreme temperatures.
Silicone
Percentage of a monocrystalline solar panel: 1.11%
The solar panel manufacturing process also uses silicone - not to be confused with the semiconducting polysilicon covered earlier in this guide.
Silicone adhesives bond the glass, frame, and backsheet. This creates a watertight and airtight seal that protects the solar cells from moisture, dust, and mechanical stress. Silicone coatings also boost the panel's UV resistance.
Although the polymer isn't directly involved in power production, its flexibility and durability in harsh weather are crucial for keeping solar panels structurally sound and long-lasting.
Glass
Percentage of a monocrystalline solar panel: 79.92%
Glass serves as the protective outer layer that shields delicate PV cells from external damage while allowing sunlight to pass through.
Solar panels use tempered glass (aka toughened glass). Tempered glass is much stronger than standard glass and can withstand the elements, including hail, wind, and extreme temperatures, making it ideal for long-term outdoor use.
The manufacturing process involves layering tempered glass on top of the solar cells during the panel assembly. A lamination process then bonds it to the cells and other layers, including the EVA encapsulant and backsheet. This ensures a tight seal that protects the cells from contaminants and mechanical stress.
Aluminium frame
This final component isn't listed in the panel's core materials breakdown table above.
That’s because the IEA PVPS doesn't consider the aluminium frame as part of the solar panel itself, despite its vital structural and protective role. Instead, it gets added at the end of the assembly process, after the PV layers, glass, and backsheet.
An aluminium frame keeps the panel safe from bumps and bangs, and makes it easy to mount. Plus, the metal is strong enough to take a beating from the elements.
The growing adoption of larger, more efficient solar panels has increased aluminium demand due to the need for stronger frames. According to the International Renewable Energy Agency in 2022, global solar capacity expansion could raise the demand for aluminium by at least 10-20% by 2050.
Although alternatives like steel are being explored for environmental reasons, aluminium remains the industry standard. It's lightweight and less likely to rust, so it's the preferred option for solar applications.
Summary
A long list of different parts make up a solar panel, and they all have a vital function. But silicon is the star performer, enabling the photovoltaic magic.
As the demand for solar grows, so do efforts to reduce the carbon footprint of solar panel manufacturing. The industry is working on ways to make processes more eco-friendly, including using safer materials and improving solar panel recycling.
If you’re wondering how much a solar & battery system could save you, answer a few quick questions below and we’ll provide you with an estimate.
FAQs
Related articles
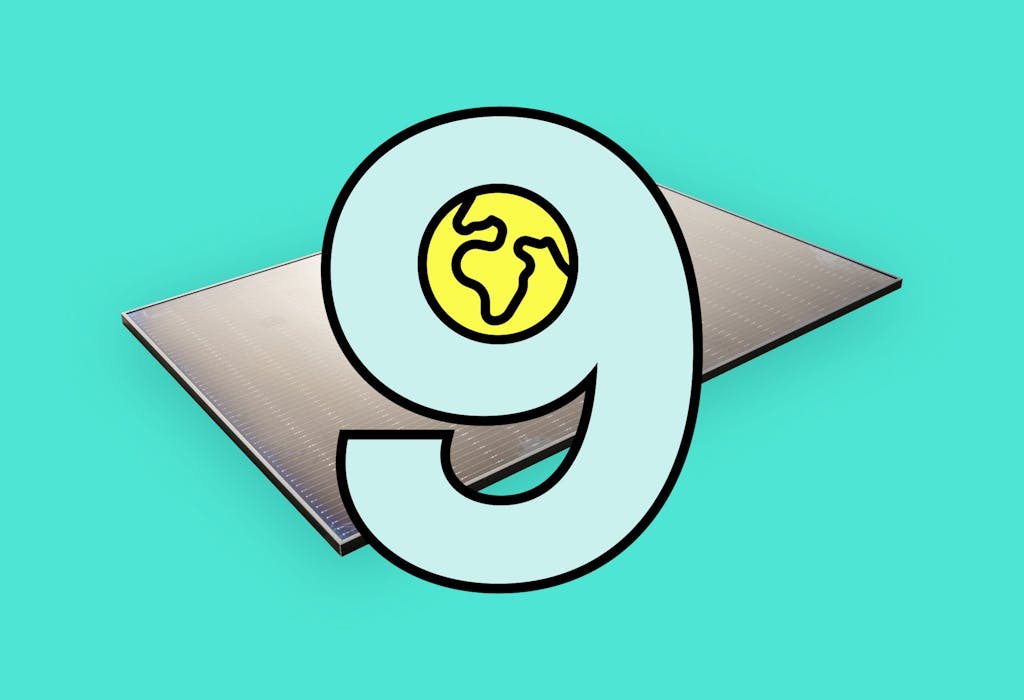
The 9 largest solar panel manufacturers in the world
Read full story

Where are solar panels made?
Read full story
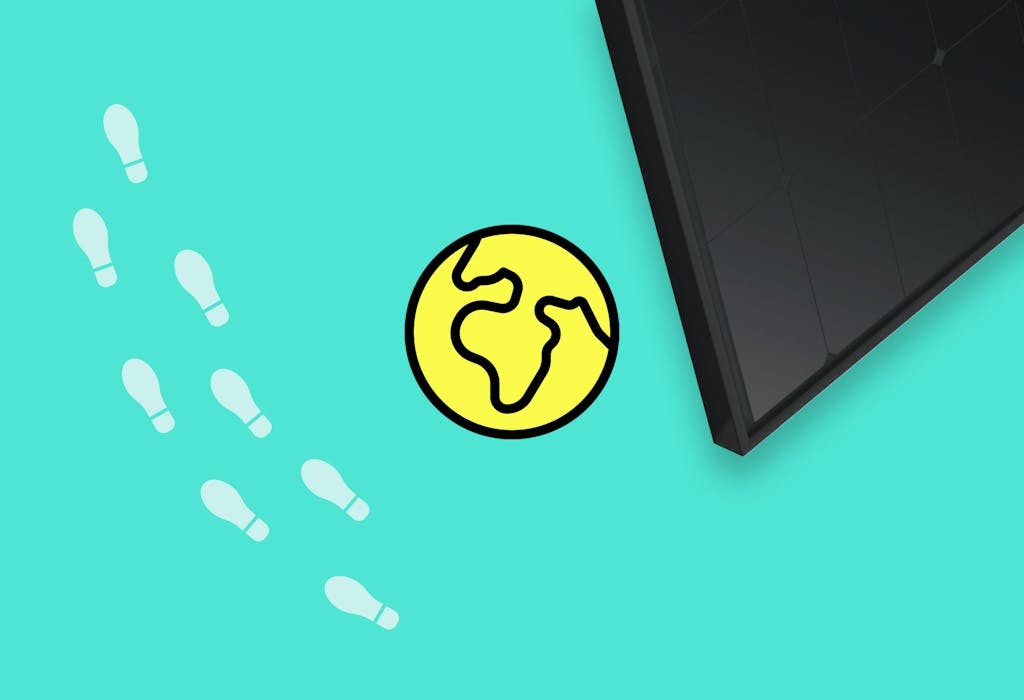
What's the carbon footprint of solar panels?
Read full story
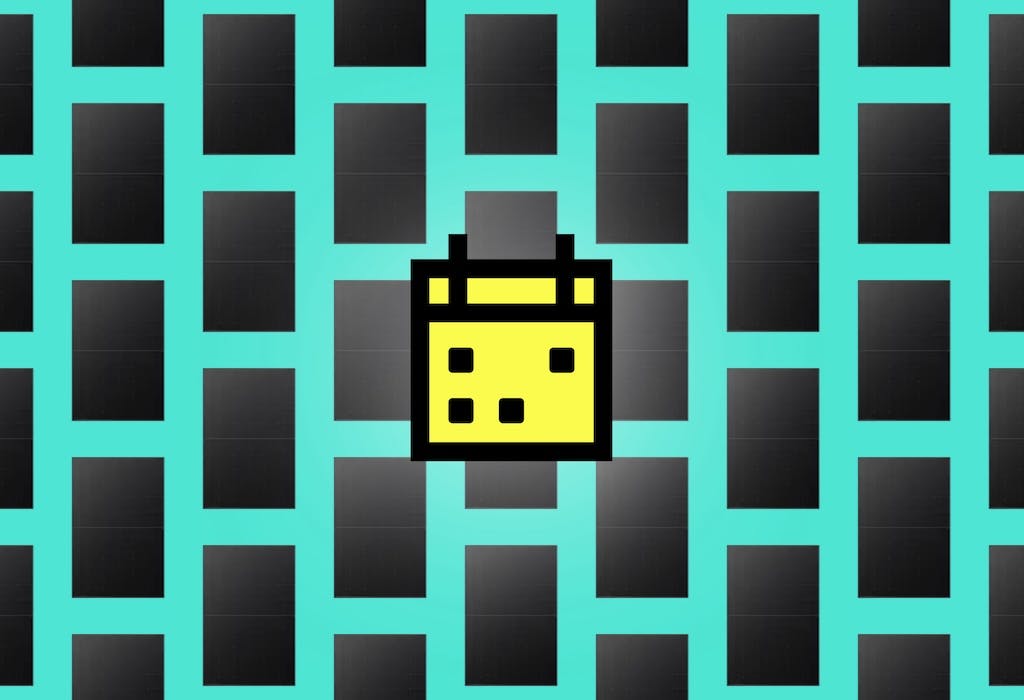
How long do solar panels last?
Read full story
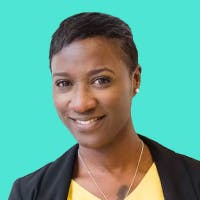
Written byMelody Abeni
Based in London, Melody is a specialist green technology writer who has been covering sustainability, climate action and ESG for the past five years, after gathering operational experience in green investing and financial services. She has written for various industry publications, including renewable technology advisor The Eco Experts, and she holds a Master’s degree in law from Birkbeck University.